While climate scientists consider sustainable aviation fuel (SAF) an important but incremental step toward meeting a 2050 carbon neutrality goal, engine and airframe manufacturers have trained their sights squarely on the fuel’s development, seeing it as an integral and enduring part of a holistic endeavor to stem climate change.
To what extent SAF will ultimately contribute to achieving net neutrality, however, remains a matter of debate. The industry’s major OEMs all voice an interest in pursuing a universal approach to curbing carbon emissions, but so far only Airbus has publicly unveiled plans to commit to such a radical solution as hydrogen power for its next clean-sheet narrowbody design. Of course, such an ambitious project will take billions of dollars in investment, not only in airframe and engine technology but in the infrastructure needed to ensure a ready supply of fuel for the airplanes.
Perhaps the most important benefit of SAF lies with its so-called “drop-in” nature, meaning, for example, that it doesn't require the development of groundbreaking new technology by engine makers and major adaptations to distribution infrastructure. ASTM-certified SAF, regardless of its source, can power any modern jet engine, meaning engine makers have to make only minimal investment aside from the cost of the engineering evaluations and testing that might occur prior to approving a new SAF.
More SAF Production Needed
Still, SAF accounts for less than 0.1 percent of all jet fuel burned by the aviation industry. Increasing that share to the point of generating any appreciable effect on the environment will depend on creating conditions that will allow for more production and distribution at a lower cost to operators. That, in itself, presents a challenge for the entire industry, one that the OEMs will need to help meet.
“As a society, we need to partner between government and industry to go much faster and accelerate the transition,” Pratt & Whitney Engineering senior fellow Dr. Michael Winter told AIN. “We're much less than 1 percent SAF production today. In order to get ahead of the curve, it's going to take cooperation and collaboration and investment in the infrastructure required.”
While that cooperation needs to lead to more supply of SAF, for example, creating a standard to allow engines to fly on 100 percent of the fuel must eventually accompany increases in production capacity, said Winter. Gaining ASTM certification for 100 percent SAF will require arriving at the proper chemical fingerprint to account for the loss of certain properties or molecules that would result from the removal of conventional jet fuel from the blend. Engine seals require a particular level of aromatics in the fuel to properly perform their intended function, for instance. Meanwhile, fuel compatibility hinges on more than its aromatics content.
“There's a lot more that goes into the standard than just the aromatics and the seals,” explained Winter. “For example, lubricity—some of the lubrication of the fuel components is provided by the fuel. Other factors like…volatility and viscosity as a function of temperature are important for altitude re-light. That's a question of safety of flight…There are some 50 parameters that need to be identical for a drop-in replacement.”
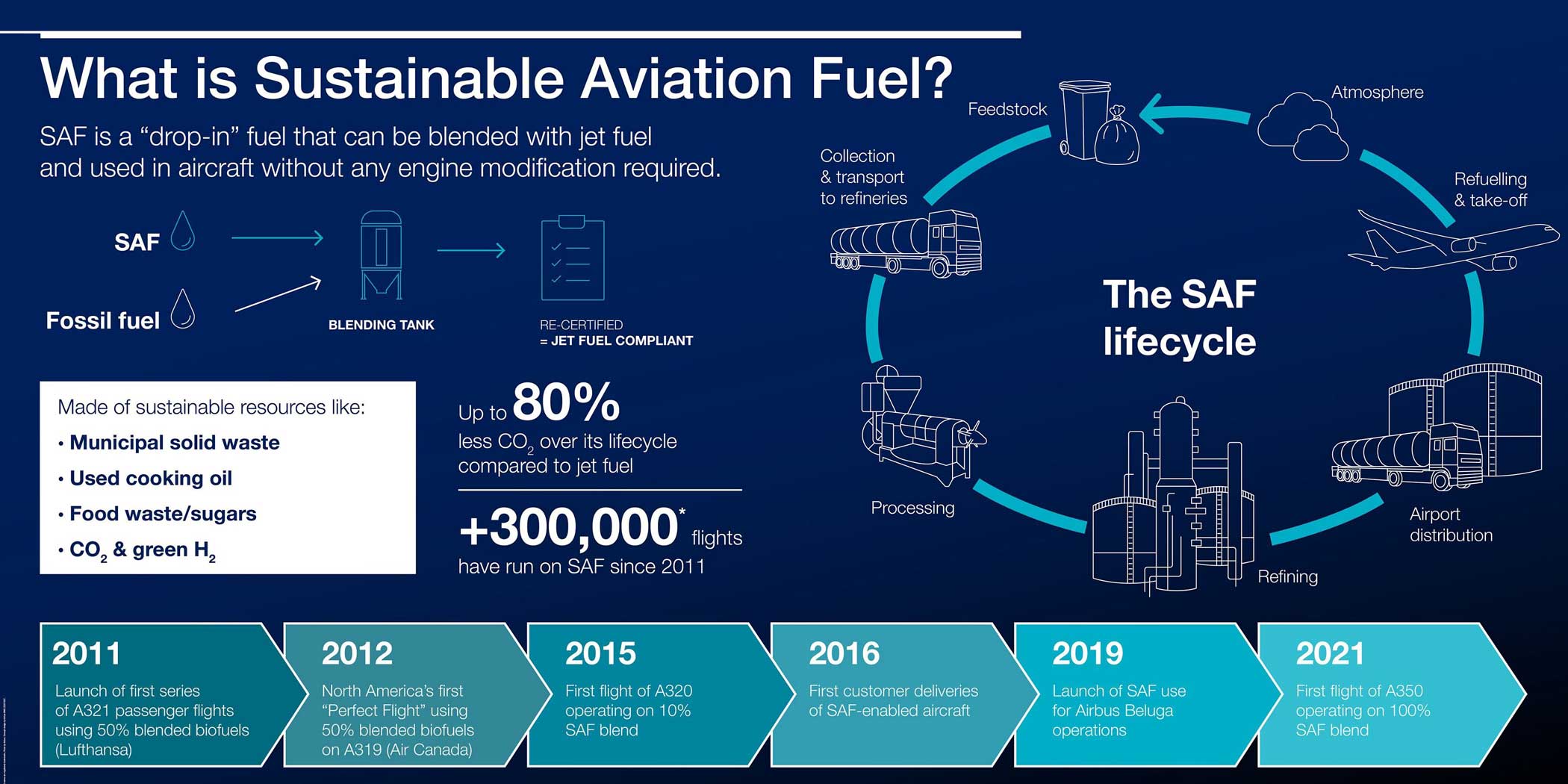
SAF Task Force Convenes
In April the Commercial Aviation Alternative Fuels Initiative (CAAFI) participated in the launch of an ASTM task force to define the standard with an aim of certifying 100 percent SAF. CAAFI executive director Steve Csonka told AIN that the coalition will prompt the exploration of several approaches to allow for the use of fully synthetic fuel, including employment of an existing, fully formulated synthetic blending component to move past the 50 percent blend now allowed. Other approaches would involve blending of other blending components; deriving an entirely new specification that would maintain compatibility with the most common ASTM specification (D1655) while using a process similar to the standard practice for the evaluation of new turbine fuels (D4054); and moving toward a compositionally based specification rather than using the individual definitions that now prevail. Csonka expressed confidence that at least one of the approaches will emerge from the process before 2026.
The chairman of the task force, GE Aviation engineering leader for aviation fuel and additives Dr. Gurhan Andac, explained that 100 percent SAF formulated from two of the seven approved pathways could technically power jet engines as a drop-in fuel today. In fact, he noted that GE has already tested and flown its engines in multiple demonstrations with both drop-in and non-drop-in 100 percent SAF since 2016.
Although fully formulated, 100 percent SAF requires an industry-approved standard—such as that set by the ASTM—before it becomes available for commercial use. “We need to define what 100 percent SAF is,” said Andac. “Even for drop-in…there are nuances. So we need to standardize 100 percent SAF, either through the modification of the current standard we have for the blends, the ASTM D7566 or by means of a new standard. So that’s the work that started at ASTM to basically accomplish that.”
Andac expressed “high confidence” that it will take two to three years to reach a standard for a 100 percent drop-in SAF.
The GE engineering leader specifically highlighted the so-called blending of blend components approach mentioned by Csonka as another promising method for meeting standards for 100 percent SAF. While a blend component on its own might not meet the ASTM standard for 100 percent SAF, mixing it with other blend components could, especially when more become available, he explained.
“So the blend component might not be, by itself, fit for 100 percent, but blends of the blend components could look very much like jet fuel and meet [the requirements]," said Andac. “Currently, that is not allowed, but with this new standardization, we are changing that. So we will open up a door to get to 100 percent drop-in either directly with some of these pathways or by blending of blend components from different pathways.”
SAF derived from the rest of the pathways that produce synthetic paraffinic kerosene (SPK) does not contain the aromatics needed for proper interaction with seals in legacy products, meaning they aren’t fleetwide compatible. Nevertheless, Andac said, the task force also intends to standardize 100 percent SPKs such as hydroprocessed esters and fatty acids (HEFA-SPK), Fisher-Tropsch (FT-SPK), and alcohol-to-jet (ATJ-SPK)—fuels derived from fats, oils, greases, waste streams, and other feedstocks—for limited fleet approval after achieving a standard for 100 percent drop-in SAF.
Andac noted that the company has already tested and flown GE engines in multiple demonstrations with both drop-in and non-drop-in 100 percent SAF since 2016.
Boeing’s 2030 Commitment
In January, Boeing promised to ensure that all its commercial airplanes can fly on and gain certification to use 100 percent sustainable aviation fuels by 2030, establishing a benchmark for its own environmental bona fides following Airbus’s 2035 hydrogen pledge. The airframer worked with airlines, engine manufacturers, and others to conduct biofuel test flights starting in 2008 and gain approval for sustainable fuels in 2011. In 2018, the Boeing ecoDemonstrator flight-test program made the world's first demonstration flight using 100 percent sustainable fuels with a 777 Freighter in collaboration with FedEx Express.
Boeing director of environmental sustainability strategy Sean Newsum explained to AIN that while the biggest challenges associated with SAF center on economics more than technology, technological advances toward the use of lower-cost feedstocks, for example, can drive down costs. Research into new feedstock sources also centers on maximizing lifecycle efficacy. For instance, Boeing participates in a program led by the U.S. National Renewable Energy Laboratory (NREL) to develop a type of SAF derived from so-called wet waste, which researchers believe can result in net-zero or even negative net emissions.
The novel process, on which NREL scientists have worked for about five years, avoids the organic waste fermenting into methane, which causes harm to the environment. Rather than allow that refuse to create greenhouse gas emissions in landfills, for example, the process essentially arrests the production of methane during fermentation and instead produces volatile fatty acids (VFA) that can be converted into SAF.
Life-cycle analysis shows that by diverting methane-producing waste from landfills, VFA-SAF could cut greenhouse emissions by 165 percent and soot by 34 percent compared with fossil fuel, according to a paper recently published in the Proceedings of the National Academy of Sciences. The study evaluated the catalytic conversion of food waste-derived VFAs to produce a paraffin SAF to meet a 10-percent “fast track” ASTM specification blend for use by Southwest Airlines in 2023. It also details how researchers improved the VFA-SAF flashpoint and viscosity to allow for a 70 percent renewable blend limit.
“We kind of pushed the boundary on what the fuel can do in terms of going to higher blend limits by further changing the chemistry to see how much renewable content you could get in the fuel, and 70 percent could do it,” explained the study’s principal investigator, Derek Vardon. “When we looked at the overall lifecycle emissions, that's where we got excited because if you're no longer taking the food waste and putting it in the landfill, the lifecycle analysis supported that you could actually get to a net-zero blend."
As for readying airplane systems for 100 percent SAF, Boeing’s Newsum characterized that task as an important but relatively modest challenge.
“There are some things we may need to do to our airplanes to ensure that we can provide 100 percent SAF compatibility,” added Newsum, referring mainly to possible adaptations to fuel systems. “We've started those studies…Again, it's a fuel system compatibility issue, not a fundamental operational issue.”
Airbus, too, continues to study the potential effects on fuel systems with a Rolls-Royce Trent-powered A350-900, which the companies began flying on 100 percent SAF in March. Airbus's Steven Le Moing told AIN that the company doesn’t expect to encounter major technical barriers, but that it can take nothing for granted. The company expects the test program to last until the end of this year.
“We need to be prepared to go beyond these [50 percent blend] limits and we need to start working on this right now,” Le Moing said. “That’s why we started to explore this journey of going beyond 50 percent. We started with the A350 quite recently and we ran other research projects to cover our different products. So we are deeply involved in that and we believe we will be ready between 2025 and 2030.”
Apart from validating technical assumptions and investigating the effects of 100 percent SAF on fuel systems and engines, Airbus considers the A350 test flights a signal to policymakers and governments of its commitment to do the work needed to meet the 2050 net neutrality goal. Further evidence, said Le Moing, lies with Airbus’s use of SAF in its internal operations. The company has powered its Beluga transports with SAF since 2019 and offers to deliver customer airplanes using SAF from its production sites in Toulouse, France; Hamburg, Germany; and Mobile, Alabama. “So once again, we're really leading by example,” remarked Le Moing.
While the company also sees its plans for a hydrogen-powered airplane as part of its commitment to sustainability, Le Moing stressed Airbus’s broad vision for meeting the challenge.
“We don’t want to oppose one solution against the other,” he said. “Of course, we are quite ambitious on hydrogen…We are also aware there are some challenges on the technical aspects of changing drastically the aircraft configuration and the external energy ecosystem we will need and also the infrastructure.”
Le Moing noted that Airbus’s hydrogen project will involve a relatively small airplane flying to a range of 2,000 nm; the company considers any possible hydrogen-powered widebody a far longer-term prospect.
Le Moing’s counterpart at Rolls-Royce Civil Aerospace, director of product development and technology Simon Burr, told AIN that Rolls has started talking with Airbus about the hydrogen project. But while noting that Rolls will not limit itself to one kind of sustainability effort, he conceded that the fuel poses “lots of challenges.”
Conversely, Burr characterized the job of readying its engines for 100 percent SAF as fairly straightforward. In fact, along with powering the Airbus A350-900 test flight on 100 percent SAF, Rolls conducted ground testing using unmixed SAF in a Trent 1000 and a Pearl 700 business jet engine, the results of which validated virtually all assumptions.
“The point is that modern engines have got synthetic seals in them so we’re not worried about the effects on nitriles and so on,” said Burr. “Our engines can deal with the subtle differences in calorific value and volumetric density. And the operability with different aromatic content was…no problem at all. And emissions, as expected—particulate emissions—were way down, which is a great thing.”
Rolls-Royce will perform its next series of tests in the autumn with a Trent 1000 fitted to a Boeing 747-200 testbed at altitude to validate, for example, re-light operability. “The other interesting thing about that, of course, is you’re testing SAF in an older airframe, [with aging seals],” noted Burr.
Rolls-Royce has run engines on fuel derived from two different sources of HEFA without any adverse effects on the hardware. But Burr was careful not to minimize the job the industry as a whole still faces. “You've got to do work,” he said. “You've got to look across the range of operating conditions plus all the attributes and then do proper testing…We’re not saying we’ve done formal testing to certify anything; we’ve shown compatibility. So there’s more to go in this space if we’re honest.”
For example, the long-term effects on hardware of burning 100 percent SAF need consideration, including thermal stability and lubricity. Burr explained that SAF shows “superior” resistance to forming gum deposits that typically come with oxidation resulting from increases in temperature. Separately, gear pumps in a jet engine get their lubrication from fuel, meaning the fuel must maintain its lubricity or risk premature wear of those parts. “I don’t see any other things you need to worry about in a jet engine,” said Burr. “If you’ve got a fuel that is thermally stable, we’re not going to be worrying about fuel system issues. Then it’s just a question about acidity and other things that have marginal effects. Within the engine itself, if you’ve got cleaner combustion, that’s kind of a good thing. But we will be exploring all of those things. We’re in the early days right now.”