A group of leading aerospace companies has joined forces to develop hybrid-electric and water-enhanced turbofan engine technology for future airliner propulsion systems. In a November 29 announcement, MTU Aero Engines, Pratt & Whitney, Collins Aerospace, Airbus, and GKN Aerospace said that work backed by the European Union’s Clean Aviation Joint Undertaking aims to increase fuel efficiency and reduce carbon dioxide emissions from short- and medium-range aircraft by up to 25 percent.
The Sustainable Water-Injecting Turbofan Comprising Hybrid-Electrics (SWITCH) project will seek to combine the MTU-led Water-Enhanced Turbofan (WET) and hybrid-electric propulsion with the existing architecture of Pratt & Whitney’s Geared Turbofan (GTF). The planned powertrain will be able to run on sustainable aviation fuel (SAF) and will also be developed to be ready use hydrogen fuel in the future.
The program is being supported by both the Clean Aviation initiative and the UK Research and Innovation (UKRI) agency. The partners did not specify the amount of funding available from government sources beyond indicating that it will run into “tens of millions” of euros.
The funding approved so far covers Phase 1 of the work through the end of 2025. This will include testing a hybrid-electric version of the GTF, as well as designing and testing the WET technology and integrating it with the rest of the powertrain. If this work achieves the anticipated results, funding will be sought for further phases of work that would get the propulsion system closer to production and service entry on an as-yet unspecified aircraft.
The WET concept recovers water vapor from the engine exhaust and re-injects it into the combustion chamber in a way that MTU says will improve fuel efficiency, as well as reducing nitrous oxide (NOx) emissions by 80 percent and also cutting contrail-forming emissions by flushing out accumulated soot from the engine. MTU is developing the system’s steam turbine and water recovery unit, with Pratt & Whitney providing a steam-injecting combustor to combine with a vaporizer from GKN and a condenser from Collins.
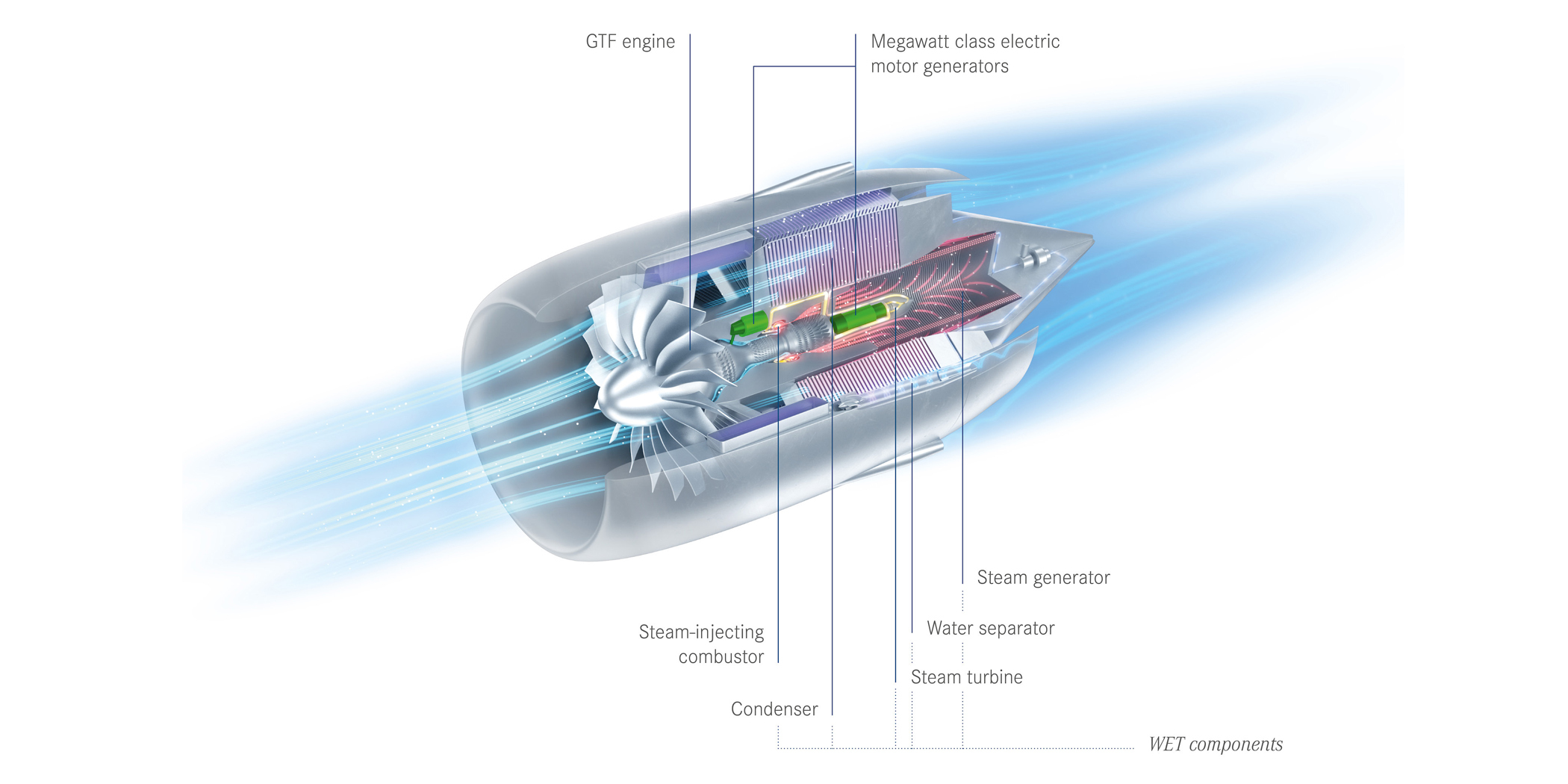
According to Claus Riegler, MTU’s senior vice president for technology and engineering, the partners aim to get the systems to technology readiness level (TRL) 4 by the end of Phase 1. Under the anticipated Phase 2 works, the goal would be to extend this to TRL 6 by 2029.
According to Riegler, one of the program’s key challenges is balancing the anticipated weight increase for the new version of the GTF with the overall improvement in power efficiency and fuel consumption. MTU expects that adding the WET technology will increase the weight of each turbofan by as much as 50 percent. MTU will work with its partners to find a new way to integrate the engines into aircraft wings so that the weight increase is more than compensated for by the gains in specific fuel consumption.
For Airbus, a hybrid-electric version of the GTF could be used for a clean-sheet aircraft design. “The aim [of SWITCH] is to explore the hybrid-electric approach and ensure that the benefits are there,” said Karim Mokaddem, the airframer’s head of electrification. “The objective is to have an entry into service not before 2030 or 2035, and it’s important to assess the benefits now and ensure that these can be achieved from the system architecture at an aircraft level.”
Under its Zero E program, Airbus is also working on plans for a hydrogen-powered airliner that would carry around 200 passengers up to 2,000 nm. In 2024, it intends to select one of three airframe concepts being evaluated and start making a technology demonstrator in 2025.
The hybrid-electric version of the GTF will use a powertrain developed by Pratt & Whitney’s Raytheon Technologies sister company Collins. This will include megawatt-class electric motor generators, as well as power electronics, high voltage DC distribution and protection, thermal management components, and a new nacelle to accommodate the components.
According to Mary Lombardo, the company’s vice president of applied research and technology, the partners aim to be ready to demonstrate the integrated powertrain at Collins’ new electric power systems laboratory in Rockford, Illinois, which is due to open in 2023 and is called The Grid. Collins’ contributions to the SWITCH project will include the U.S.-based group’s facilities in France, Germany, Italy, Ireland, and the UK.
GKN will help to develop engine structures required for the hybrid-electric version of the GTF, including integrated electric machines and heat exchangers. Henrik Runnemalm, vice president of the group’s Global Technology Center in Sweden said the SWITCH team will have access to its “hot” test rig in Trollhättan, and its Fokker subsidiary in the Netherlands will provide high-voltage electrical wiring.
The SWITCH project will also be backed by several other unnamed aerospace companies, as well as universities and research organizations from the U.S. and 10 European countries. The latter will include the Aristotle University of Thessaloniki in Greece, Sweden’s Chalmers University of Technology, Germany’s University of Stuttgart, and the DLR German Aerospace Center.
The Clean Aviation initiative is a public-private partnership co-funded by the European Union, the aerospace industry, and various research institutions. It is part of a wider effort to achieve net zero emissions in the air transport industry by 2050.