Airbus’s multi-path approach to decarbonization took a new direction last week as the company highlighted recent work on superconductivity technology. During its two-day Sustainability Summit held in Toulouse and Munich, the airframer said it has joined with the European Laboratory for Particle Physics in a demonstrator program aimed at promoting the adoption of superconductivity and cryogenics in airborne electrical distribution systems.
The Swiss laboratory, which operates under its French acronym CERN, bases most of its research on its subterranean Large Hadron Collider, which is the world’s largest and highest-energy particle collider. Its new project with Airbus, called the Superconductor for Aviation with Low Emissions (SCALE), will evaluate how engineers can deploy superconductors to achieve greater energy efficiency for future aircraft systems.
The project marks the latest in a series of studies led by Airbus UpNext, a company subsidiary created to identify future aerospace trends and technology concepts and evaluate them as potentially viable products. The division aims to accelerate traditional research cycles, develop proof of concepts, complete testing with scale and speed, and deliver what Airbus calls critical learning within a two- to three-year timeframe.
The initiative aims to develop and test a 500-kilowatt generic superconductor cryogenic powertrain by the end 2025. CERN plans to design, construct, and test SCALE using Airbus UpNext specifications and the laboratory’s technology. The demonstrator consists of a DC link (cable and cryostat) with two current leads and the cooling system uses gaseous helium.
Several electric propulsion developers already conduct work on tapping the potential of high-performance superconductors for new aircraft. They include UK-based start-up Mako Aerospace, which is developing its Forerunner family of ducted fan engines for new airliners.
Cryogenics' 'Great Potential'
During the Sustainability Summit, Airbus UpNext CEO Sandra Bour-Schaeffer described the “great potential” of the use of cryogenics to aid electrical conductivity in power trains, including distribution, power electronics, cooling systems, and electrical motors.
“Cryogenic [technology] is just using the benefit of extremely low temperatures and here we're talking about minus 150 degrees Celsius,” she explained. “But as you have heard, we are storing liquid hydrogen on board, which means we have this source readily available. And if you use traditional electronics components and systems at a cryogenic temperature, you reduce the electrical losses and, therefore, you improve the performance. And if we go a step further into the conducting word—and here we're talking around minus 190 degrees—it's even more interesting because the electrical resistance literally becomes zero and all of a sudden you are capable of transporting megawatts in small cables.”
Although not all of the advances from the collaboration will reach maturity in time for the launch of Airbus’s ZeroE hydrogen-powered aircraft in 2027 or 2028, Bour-Schaeffer identified power distribution as one component of the program that could conceivably find its way onto the new aircraft. “Clearly, there will be a different timeline associated with [the electric motor],” she explained. “We believe that electronic distribution could be mature very soon. If we look into a few megawatt cryogenic superconducting motor, it'll be further down to the line.”
Airbus UpNext has already embarked on a related study into the feasibility of the technology for fully electric and hybrid-electric aircraft called ASCEND (Advanced Superconducting and Cryogenic Experimental Powertrain Demonstrator), said Bour-Schaeffer. One of the major challenges of scaling up electric propulsion to larger aircraft relates to power-to-weight ratio. Today’s electrical systems do not meet the necessary power requirements without adding excess weight to the aircraft. However, superconducting technologies have begun to emerge as a possible solution, notably by increasing power density in the propulsion chain while significantly lowering the mass of the distribution system.
According to Bour-Schaeffer, engineers have finished the related technical analyses and have embarked on the program’s manufacturing phase at its Munich-area facilities, where they expect to achieve “power-on” near the middle of next year.
CERN Lab's Participation Critical
Bour-Schaeffer explained the critical nature of CERN’s participation given the highly advanced instrumentation it brings to measure such phenomena as hydrogen leakage. Appearing with her at the summit, CERN director of finance and human resources Raphael Bello noted that the laboratory spends about a third of its $1.2 billion annual budget on research and development as well as instrumentation because, he explained, “we are not theoreticians, we are mainly engineers and technicians to develop the infrastructure.”
“First of all, we do believe that CERN has something to provide to Airbus and vice-versa I would say because it happens that we try to also learn from our partners and not lecture them,” said Bello. “The second rationale, I would say, is because we are sharing the same values.
“We do believe that CERN has the capacity to provide its technologies to Airbus UpNext, in particular, to create a new demonstrator for next year. This demonstrator will create ceilings to support aircraft power distribution systems in general, and then, of course, this would be the first step of our collaboration. Hopefully, there will be many other new steps in the journey to perhaps include other partners, other stakeholders, including European stakeholders such as the European Commission and other industry partners to push again the limits of our technology.”
Meanwhile, the Airbus UpNext team continues to orchestrate multiple other approaches to driving carbon emissions out of aviation. They include advocating for the use of continuous climb and descent paths to aid in fuel burn efficiency in airliners. The company demonstrated the tactic when it flew a party of aviation journalists from Toulouse to Munich on November 29.
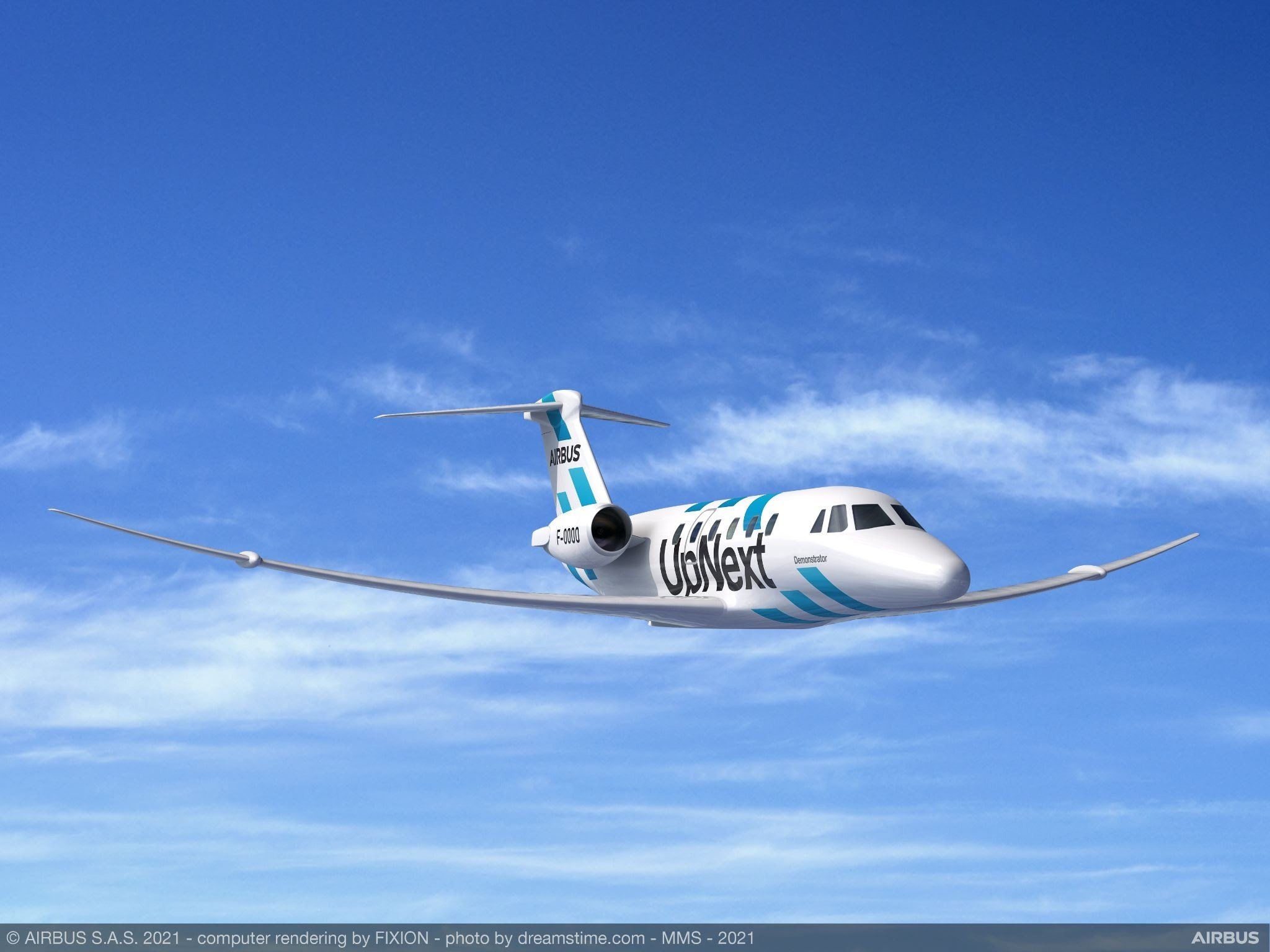
In another initiative aimed at improving the efficiency of air traffic management, the Airbus “Fello’fly” demonstrator program has taken inspiration from the way migrating geese fly in close v-shaped formations to harness energy from the wake of the leading bird. Airbus conducted a demonstration flight involving A350s flying from Toulouse to Montreal in November 2021. Bour-Schaeffer told a Royal Aeronautical Society conference in London on November 29 that the Airbus UpNext team demonstrated how “surfing the air upwash” from the leading aircraft at a safe distance of 1.6 nm could reduce fuel burn by at least 5 percent.
In 2024, Airbus expects to start test flights with its Xwing future wing demonstrator using a converted Cessna Citation VII business jet. The work on the “extra-performing wing” started in September 2021 and is part of the manufacturer’s Wing of Tomorrow program. In another project based on the biomimicry approach to learning from nature, Airbus expects to show how active control techniques can optimize the use of an aircraft’s wing in the same way that a soaring eagle adapts the shape, span, and surface of its wing and feathers.