When Parker Hannifin acquired Meggitt PLC and officially made it part of Parker Aerospace in September of 2022, the new partnership nearly doubled the size of Parker Aerospace. With an enhanced portfolio of complementary products and services and a broader and deeper suite of solutions for aircraft and aeroengine components and systems, the addition of Meggitt significantly strengthens Parker’s position as a global leader serving the aerospace and defense industries. The combination also expands Parker’s aftermarket support, delivering in-region support through regional hubs with expanded expertise.
Parker Aerospace is growing key technologies for the future, with continued R&D investment in next-generation core products and advanced technologies to support sustainable aviation. Tracy Rice, group vice president, technology and innovation for Parker Aerospace explains, “Parker and Meggitt both have a proud engineering heritage and a long history of innovation. Our focus remains on providing a premier customer experience, and we are now even better positioned to play a pivotal role in meeting the challenges of sustainable aviation head on. We have technologies – some in service now, others in development – that lead to lighter, more efficient aircraft and reduced fuel burn, that will support the next generation of aircraft engines and that will help enable sustainable aviation propulsion. These technologies cover nearly the entire spectrum of aviation.”
There are several areas in which Parker is focusing its engineering talents to impact the next generation of sustainable aviation:
Safety systems
Aircraft fire suppression systems are evolving with the introduction of environmentally friendly suppressive agents to replace the ozone-depleting agents currently in use. Parker is at the forefront of this technology change with its own patented, halon-free suppressive agent named VERDAGENT®. It is specifically designed for use in cargo suppression yet will also work for engine and APU applications. Parker is also leading the way in the certification of the fire extinguishing agent CF3I for engine/APU applications.
Electrification
More-electric aircraft are becoming even more so as the application of electric and localized power is reducing weight and increasing onboard efficiency. A sampling of innovations in this area consists of:
Lithium batteries – Parker offers an energy storage solution that is engineered to be a dependable, lightweight option for longer range, safety, and power. With a weight that is up to 50% less than NiCad or lead acid systems, lithium batteries provide an efficient and effective way to store energy. And, since lithium chemistry uses no cadmium, the technology is more eco-friendly.
Hydraulic powerpacks – Scalable to meet targeted power demands from nose to tail, fully contained hydraulic powerpacks optimize power distribution, lower weight, and reduce costs. Parker’s hydraulic powerpacks utilize power-on-demand technology that can significantly reduce power consumption and automatically deliver smart power when and where it is needed. These fully integrated systems with power control electronics feature plug-and-play interfaces that simplify installation and maintenance.
Ultralow-power ice protection systems – This innovation uses high-frequency vibration to induce strain and overcome the adhesive strength of ice on the airflow surface. This process removes the ice from the protected surface by shattering it rather than melting it, resulting in a technology that uses up to 90% less energy. Further, by reducing demand on the engine for bleed air, engine efficiency is enhanced.
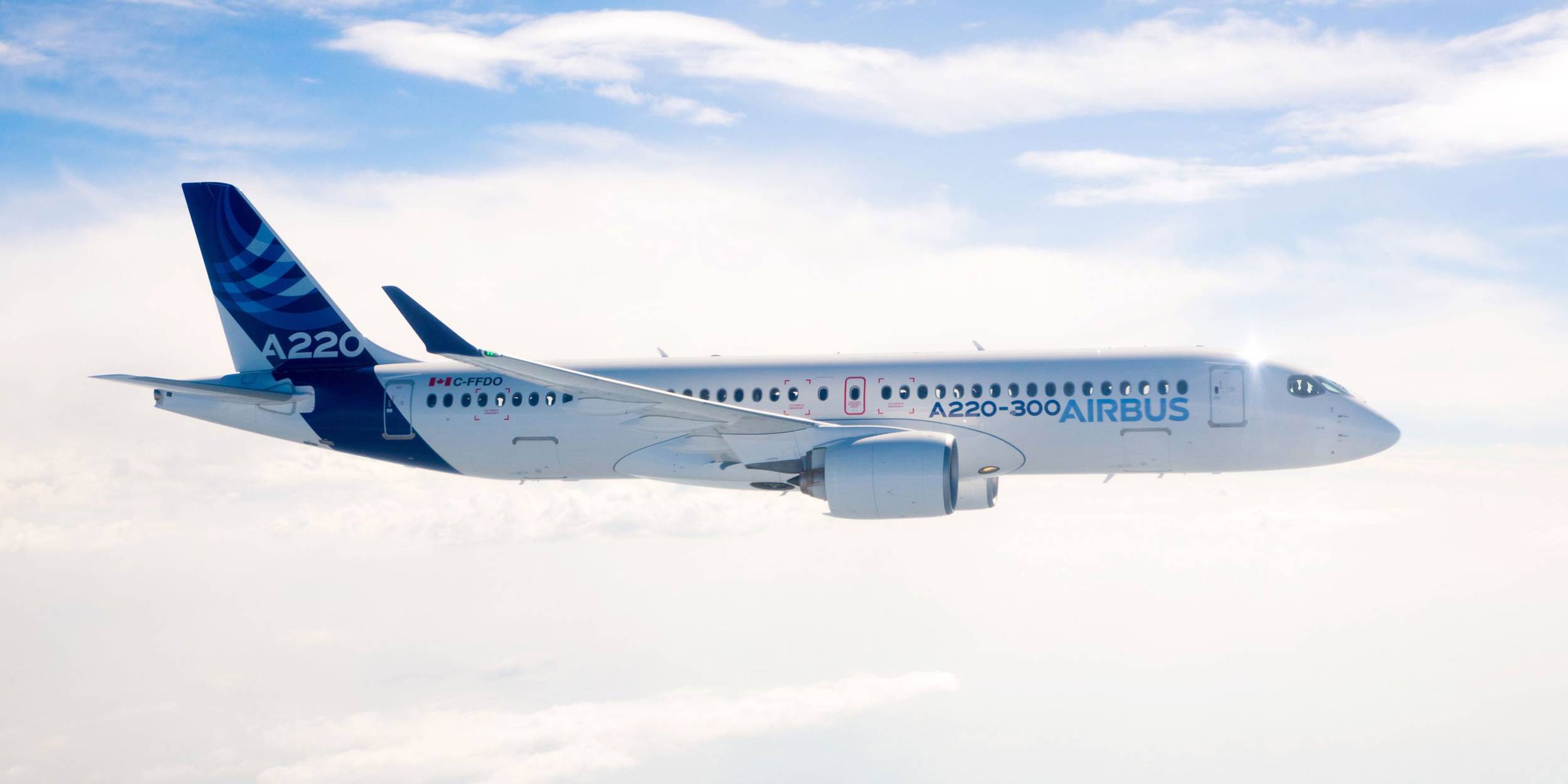
Electric braking systems
This first-of-its-kind braking innovation is in service today on the Airbus A220. By integrating brake-by-wire technology with an electromechanical operating system, the Ebrake® achieves high performance while being more compact and efficient compared to traditional hydraulic brake systems. Carbon wheels from Parker also lighten aircraft wheel and brake systems, further boosting efficiency.
Composites
Novel application of composite materials, along with the development of manufacturing technologies to help bring these products to the marketplace, have resulted in weight-saving efficiencies.
VBV composite equipment – These close-molded components for flight-critical rotating and non-rotating applications are found on several high-rate commercial and military platforms, including the F135 and LEAP engines. A unique compression molding process allows intricate designs and shapes, using high-temperature composite materials to replace precision-machined metals, resulting in weight, maintenance and performance improvements.
Composite oil reservoirs – Designed for aviation engines, they can offer 20% weight savings over titanium and aluminum tanks and reductions of up to 50% versus stainless steel. These lightweight reservoirs can provide significant fuel and emissions savings over the life of the product and result in a low total cost of ownership. In addition, the composite fabrication process can yield more complex shapes to fit into unusual envelope contours.
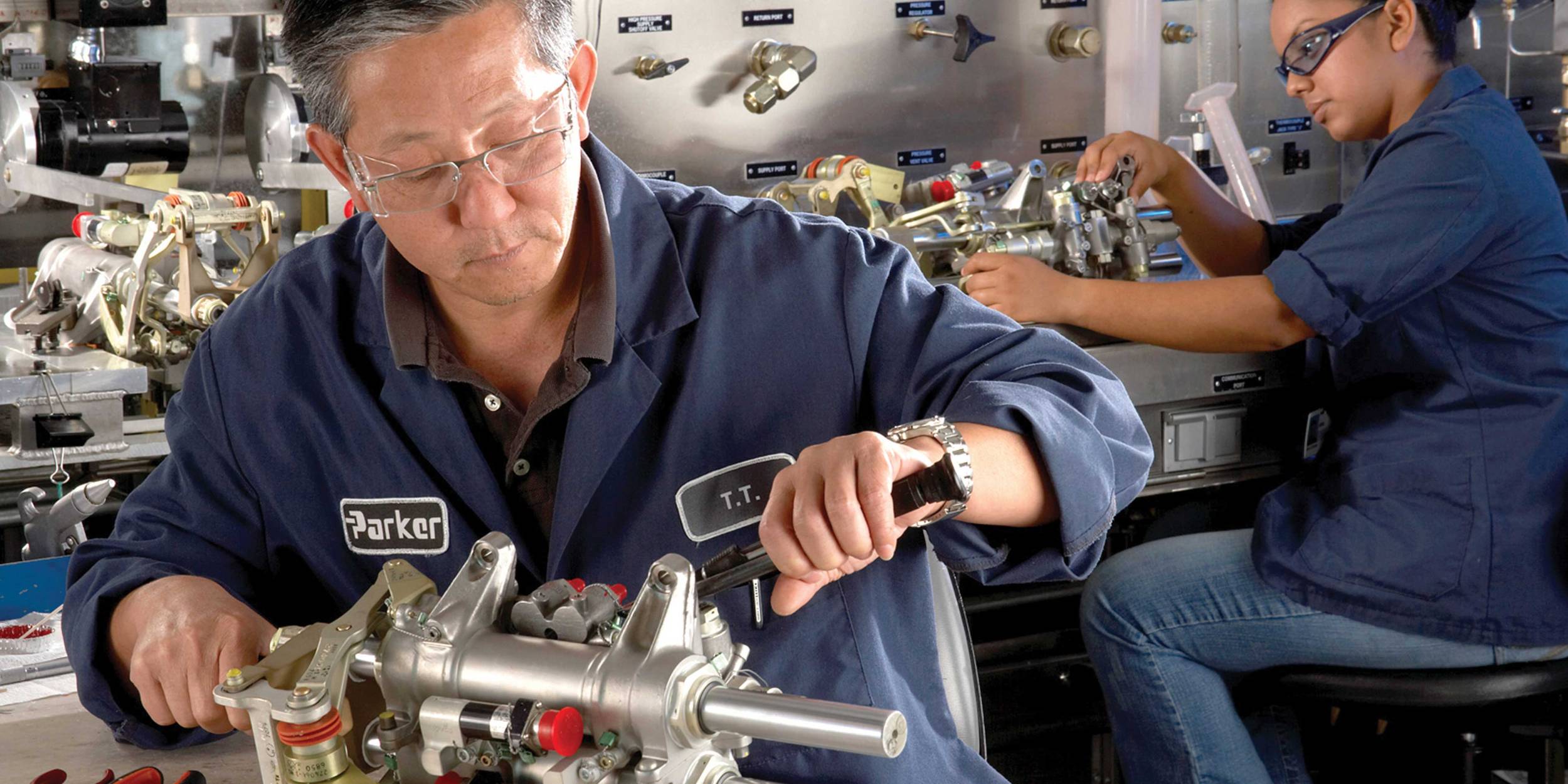
Thermal management
As aircraft rely more on advanced power electronics and engineering envelopes are shrinking to save weight and space, thermal management becomes more critical.
Advanced Macrolaminate™ liquid cold plates – These innovations enable extremely high-power densities, providing focused cooling in envelopes as small as 1/8-inch thick. Offering thermal performance far exceeding traditional designs, they can be flat or configured to conform to a shape and can also double as mounts, enclosures or EMI/RFI shielding. Designed to withstand harsh environments, Macrolaminate™ liquid cold plates manage high heat flux in an efficient package. These devices are optimized for SWAP and deliver excellent thermal performance in both single- and two-phase applications.
Structural heat exchangers – Offering optimal heat transfer when space is at a premium and weight and drag must be minimized, structural heat exchangers integrate the thermal management solution into an existing structure on an engine or other heat source. Fabricated using the Macrolamination™ process to attain superior mechanical and thermal properties, these heat exchangers can achieve a high level of load-bearing capability and enable advanced architectures while increasing heat sink, limiting weight and drag impact, and conforming to present envelopes.
Inclined heat exchangers – The unique design of these heat exchangers acts as an enabler for the introduction of the new power gearboxes and slim-line nacelles that are at the center of engine manufacturers’ efforts to deliver a significant improvement in specific fuel consumption for the next generation of engines.
To accommodate the new fan and gearbox design, OEMs are slimming down the nacelle, compromising the available space for equipment traditionally housed in the nacelle mounted off the engine fan case. This radical engine design presents significant challenges for thermal systems, as the new power gearbox doubles the heat load to the oil that the heat exchangers cool. Additionally, the slim-line nacelle means that thermal systems now need to be mounted on the core case, a more spatially constrained part of the engine. Patented inclined heat exchanger systems are showing a greater than 40% performance improvement. The system’s 0.3% reduction in fuel burn amounts to a yearly reduction of 200 tons of CO2 emissions per aircraft.
Other vital innovations
Parker is bringing its considerable engineering strength to bear on its customers’ challenges in other areas, such as:
Fuel tank inerting systems – Parker is the global leader in this critically important area, providing fully integrated pallet inerting systems as well as developing new technologies to reduce weight and continually improve safety, reliability, and cost of ownership.
Hydraulic and lubrication systems – Innovative fluid pumping solutions, such as the Next-Gen pump family and ePump, offer weight savings and efficiency gains. Filtration technologies, such as Porofelt® filtration media, enhance fluid cleanliness and boost system life.
Sensing and data equipment – Parker’s optical pressure and temperature sensing for lightweight combustion dynamics monitoring is the first of its kind and offers accurate, reliable, and responsive performance in extreme environments.
For more information on how Parker is enabling the next generation of sustainable aircraft, visit parker.com/aerospace.