When Leonardo opens its training academy at its Northeast Philadelphia Airport facility—planned for the summer of 2020—it will be home to the first level D full-flight tiltrotor simulator. But until then, the closest thing to actually flying the AW609 is the System Integration Simulator (SiSL) used by engineers and test pilots to explore and validate modifications before they go onto the aircraft. It is also used to develop and rehearse flight-test programs, among other duties. The cockpit section of the SiSL is located at the far end of a very large room, mounted on a fixed-base raised stage and facing a 180-degree wrap-around visual screen, approximately 15 feet high. The remainder of the room is filled on one side with racks of computers and on the other, various engineering and operating work stations.
Dan Wells, one of Leonardo’s team of test pilots, is going to give me my first lesson in flying tiltrotors. Wells has been with the program since the early days and has amassed 690 hours on the 609. Before this, he was a graduate of the U.S. Naval Test Pilot School at Patuxent River, Maryland, and flew the V-22 and CV-22, both with the military and as a production test pilot with Bell.
Wells guides me around the cockpit of the SiSL, which is equipped to the standard of the third test aircraft, AC3. That includes a three-screen Collins Pro Line 21 EFIS, two smaller radio/nav control panels, and an integrated standby horizon. Production-configured versions, starting with AC4, will fly with the Collins Pro Line Fusion. On the Pro Line 21 flight deck, each pilot has a PFD and the third screen is an MFD with engine and system instruments. The SiSL's appearance is very much that of a helicopter flight deck, with its large transparencies (including chin windows) and collective and cyclic controls. And as in a helicopter, the P1 command seat is on the right. But the pressurization controls on the center console and the flap lever in front of the P2 seat tell you that this is something different.
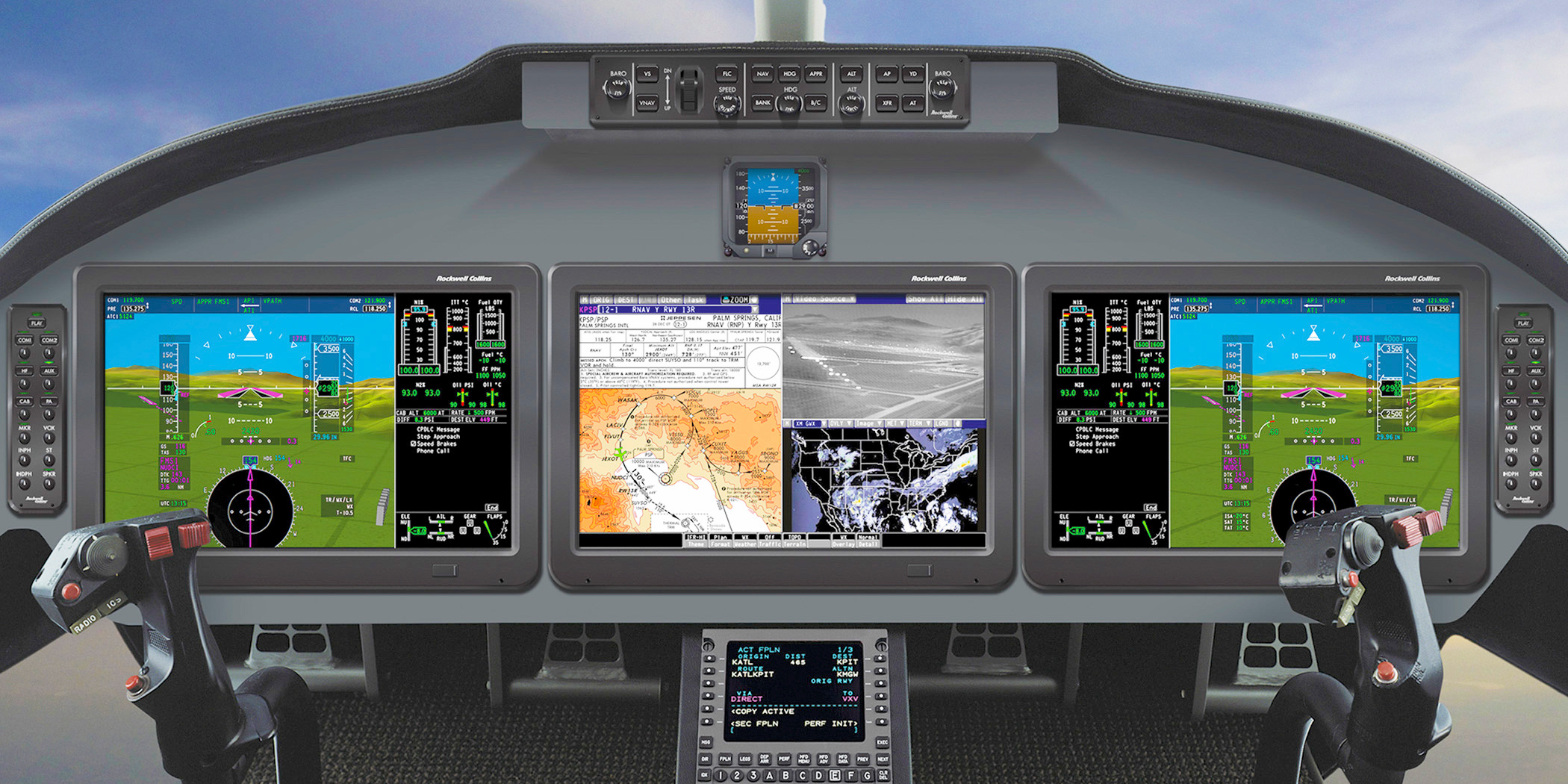
Normal Operations
When we climb into the simulator, our virtual AW609 is positioned at the end of Runway 26L at Vancouver, British Columbia, with engines running and prop-rotors turning on what looks like a nice CAVOK day. We get straight into it with a normal helicopter takeoff into the hover. I am fresh from flying the TH-119 prototype, so my mind is in rotary mode and the takeoff feels entirely normal, with the engine nacelles pointed upwards.
Using the trim release button on the cyclic, I can make small corrections to keep us stationary above the threshold. I use the collective to adjust the hover height, aiming for a high hover of around 20 feet, which I read off the radar altimeter on the PFD. The flaps have five settings—AUTO, 0 degrees, 20 degrees, 40 degrees, and FULL. We selected the AUTO setting to ensure that, in the hover, they extend to FULL to minimize the wing area to reduce the effects of downwash. A spot turn is straightforward, with only small flight control inputs required. The chin windows provide excellent visual references.
As we line up with the runway, Wells briefs me on the first takeoff. The engine nacelles are controlled by a knurled thumbwheel on the collective and have three preset angles: 75 degrees, 50 degrees, and 0 degrees. Pushing the control fully forward selects the first stop at 75 degrees and the nacelles rotate at a rate of 3 degrees per second. The rotation of the nacelles tilts the thrust vector forward to provide acceleration. In a helicopter, this is achieved by lowering the nose using the cyclic. Having tilted the thrust vector away from the vertical, power must be added to prevent losing altitude, achieved quite naturally using the collective. The aircraft accelerates briskly while I maintain a level attitude with the stick.
On the round-dial airspeed indicator in the top left corner of the PFD, a white arc appears, looking similar to the flap operating range on a fixed-wing ASI. It displays the speed range appropriate to the nacelle angle. At 75 degrees of tilt, the maximum speed during conversion, known as Vcon, is 90 knots, a limit based on loads on the prop rotors. As we approach this speed, I push the nacelle angle controller forward to move the nacelles to their 50-degree position, and the arc moves to display a minimum speed of 94 knots and a max of 130 knots. The wing has begun developing lift, and the flaps are automatically retracting.
After less than 90 seconds in the hover, we rotate the nacelles to 0 degrees, which coolly brings the starboard nacelle and prop rotor into my peripheral vision. The flaps have fully retracted, and without having made any conscious transition, I am now flying a fixed-wing aircraft at 220 knots indicated airspeed. We briefly level at 3,000 feet and set up for a stall, which is very conventional, reducing power with the collective and maintaining pitch attitude with the cyclic.
One change that has occurred is that once the nacelle angle is at 0 degrees, the force trim is no longer functional. All trim changes are effected using a cone-hat thumb control, but as with everything that has happened thus far, it feels perfectly intuitive. The SiSL has no motion, but the visuals show a low-speed buffet and the nose drops at the stall. I apply power and hold a pitch of around five degrees nose down. The aircraft recovers quickly and we turn back to the airfield.
The first approach is to the hover and at 1,500 feet AAL (above airfield level), and a speed of 120 knots, I bring the nacelles to 50 degrees. We start to slow using a sight picture similar to that in a twin-engine helicopter. Progressively reducing speed and increasing the nacelle angle, I arrive over the threshold. Raising the nose slightly reduces the groundspeed to zero, and coming to a hover with the nacelles vertical, we settle back onto the runway. Rolling takeoffs and landings improve payload and are easily accomplished using a nacelle angle of 82 degrees. On touchdown, transitioning to 95 degrees brings the aircraft to a swift stop without any braking.
Engine Failures
The next step is to explore single-engine handling, and the first maneuver we try is an engine failure during a vertical takeoff. As in a twin-engine helicopter, the takeoff decision point (TDP) is the rotation at a height of around 60 feet. As we climb vertically, Wells brings back the power on one engine. I call "reject" and lower the lever to return to the ground and then cushion the touchdown by increasing power to a “soft stop.” The fly-by-wire has automatically adjusted the collective to allow 30 seconds of additional power at the one engine inoperative (OEI) takeoff limit.
For the next takeoff we continue at TDP. Wells fails the engine, and, again without having to look inside the cockpit, I pull the collective to the soft stop to give takeoff power. We climb away, rotating the nacelles on the speed schedule. After 30 seconds, the collective automatically eases down to limit the OEI power to a two-minute maximum and then further reduces to max continuous power. All the stops can be overridden if more power is required.
The 30-second OEI limit of approximately 2,500 shp is designed such that it can be used three times before maintenance action is required. This provides enough power for a takeoff, a missed approach, and a landing. We flew the single-engine landing as a run-on landing at around 40 knots with the nacelles at 82 degrees, bringing me to an end of a very enjoyable hour's flight.
My overriding impression of flying the AW609 is that it is a remarkably intuitive machine to handle and moves almost seamlessly between helicopter and fixed-wing mode. Although I had the advantage of having flown both helicopters and fixed-wing aircraft for many years, I believe that pilots from both backgrounds will have little difficulty converting to a tiltrotor, with a rotary-wing pilot perhaps having a slight advantage.
When Leonardo opens its training academy at its Northeast Philadelphia Airport facility—planned for the summer of 2020—it will be home to the first level D full-flight tiltrotor simulator. But until then, the closest thing to actually flying the AW609 is the System Integration Simulator (SiSL) used by engineers and test pilots to explore and validate modifications before they go onto the aircraft. It is also used to develop and rehearse flight-test programs, among other duties. The cockpit section of the SiSL is located at the far end of a very large room, mounted on a fixed-base raised stage and facing a 180-degree wrap-around visual screen, approximately 15 feet high. The remainder of the room is filled on one side with racks of computers and on the other, various engineering and operating work stations.
Dan Wells, one of Leonardo’s (Booth 5536) team of test pilots, is going to give me my first lesson in flying tiltrotors. Wells has been with the program since the early days and has amassed 690 hours on the 609. Before this, he was a graduate of the U.S. Naval Test Pilot School at Patuxent River, Maryland, and flew the V-22 and CV-22, both with the military and as a production test pilot with Bell.
Wells guides me around the cockpit of the SiSL, which is equipped to the standard of the third test aircraft, AC3. That includes a three-screen Collins Pro Line 21 EFIS, two smaller radio/nav control panels, and an integrated standby horizon. Production-configured versions, starting with AC4, will fly with the Collins Pro Line Fusion. On the Pro Line 21 flight deck, each pilot has a PFD and the third screen is an MFD with engine and system instruments. The SiSL's appearance is very much that of a helicopter flight deck, with its large transparencies (including chin windows) and collective and cyclic controls. And as in a helicopter, the P1 command seat is on the right. But the pressurization controls on the center console and the flap lever in front of the P2 seat tell you that this is something different.[inline-image="198786"]
Normal Operations
When we climb into the simulator, our virtual AW609 is positioned at the end of Runway 26L at Vancouver, British Columbia, with engines running and prop-rotors turning on what looks like a nice CAVOK day. We get straight into it with a normal helicopter takeoff into the hover. I am fresh from flying the TH-119 prototype, so my mind is in rotary mode and the takeoff feels entirely normal, with the engine nacelles pointed upwards.
Using the trim release button on the cyclic, I can make small corrections to keep us stationary above the threshold. I use the collective to adjust the hover height, aiming for a high hover of around 20 feet, which I read off the radar altimeter on the PFD. The flaps have five settings—AUTO, 0 degrees, 20 degrees, 40 degrees, and FULL. We selected the AUTO setting to ensure that, in the hover, they extend to FULL to minimize the wing area to reduce the effects of downwash. A spot turn is straightforward, with only small flight control inputs required. The chin windows provide excellent visual references.
As we line up with the runway, Wells briefs me on the first takeoff. The engine nacelles are controlled by a knurled thumbwheel on the collective and have three preset angles: 75 degrees, 50 degrees, and 0 degrees. Pushing the control fully forward selects the first stop at 75 degrees and the nacelles rotate at a rate of 3 degrees per second. The rotation of the nacelles tilts the thrust vector forward to provide acceleration. In a helicopter, this is achieved by lowering the nose using the cyclic. Having tilted the thrust vector away from the vertical, power must be added to prevent losing altitude, achieved quite naturally using the collective. The aircraft accelerates briskly while I maintain a level attitude with the stick.
On the round-dial airspeed indicator in the top left corner of the PFD, a white arc appears, looking similar to the flap operating range on a fixed-wing ASI. It displays the speed range appropriate to the nacelle angle. At 75 degrees of tilt, the maximum speed during conversion, known as Vcon, is 90 knots, a limit based on loads on the prop rotors. As we approach this speed, I push the nacelle angle controller forward to move the nacelles to their 50-degree position, and the arc moves to display a minimum speed of 94 knots and a max of 130 knots. The wing has begun developing lift, and the flaps are automatically retracting.
After less than 90 seconds in the hover, we rotate the nacelles to 0 degrees, which coolly brings the starboard nacelle and prop rotor into my peripheral vision. The flaps have fully retracted, and without having made any conscious transition, I am now flying a fixed-wing aircraft at 220 knots indicated airspeed. We briefly level at 3,000 feet and set up for a stall, which is very conventional, reducing power with the collective and maintaining pitch attitude with the cyclic.
One change that has occurred is that once the nacelle angle is at 0 degrees, the force trim is no longer functional. All trim changes are effected using a cone-hat thumb control, but as with everything that has happened thus far, it feels perfectly intuitive. The SiSL has no motion, but the visuals show a low-speed buffet and the nose drops at the stall. I apply power and hold a pitch of around five degrees nose down. The aircraft recovers quickly and we turn back to the airfield.
The first approach is to the hover and at 1,500 feet AAL (above airfield level), and a speed of 120 knots, I bring the nacelles to 50 degrees. We start to slow using a sight picture similar to that in a twin-engine helicopter. Progressively reducing speed and increasing the nacelle angle, I arrive over the threshold. Raising the nose slightly reduces the groundspeed to zero, and coming to a hover with the nacelles vertical, we settle back onto the runway. Rolling takeoffs and landings improve payload and are easily accomplished using a nacelle angle of 82 degrees. On touchdown, transitioning to 95 degrees brings the aircraft to a swift stop without any braking.
Engine Failures
The next step is to explore single-engine handling, and the first maneuver we try is an engine failure during a vertical takeoff. As in a twin-engine helicopter, the takeoff decision point (TDP) is the rotation at a height of around 60 feet. As we climb vertically, Wells brings back the power on one engine. I call "reject" and lower the lever to return to the ground and then cushion the touchdown by increasing power to a “soft stop.” The fly-by-wire has automatically adjusted the collective to allow 30 seconds of additional power at the one engine inoperative (OEI) takeoff limit.
For the next takeoff we continue at TDP. Wells fails the engine, and, again without having to look inside the cockpit, I pull the collective to the soft stop to give takeoff power. We climb away, rotating the nacelles on the speed schedule. After 30 seconds, the collective automatically eases down to limit the OEI power to a two-minute maximum and then further reduces to max continuous power. All the stops can be overridden if more power is required.
The 30-second OEI limit of approximately 2,500 shp is designed such that it can be used three times before maintenance action is required. This provides enough power for a takeoff, a missed approach, and a landing. We flew the single-engine landing as a run-on landing at around 40 knots with the nacelles at 82 degrees, bringing me to an end of a very enjoyable hour's flight.
My overriding impression of flying the AW609 is that it is a remarkably intuitive machine to handle and moves almost seamlessly between helicopter and fixed-wing mode. Although I had the advantage of having flown both helicopters and fixed-wing aircraft for many years, I believe that pilots from both backgrounds will have little difficulty converting to a tiltrotor, with a rotary-wing pilot perhaps having a slight advantage.