Maglev Aero is taking a radically different approach to distributed electric propulsion for new aircraft, having recently gone public with its plans for what it calls its Hyperdrive system. The Boston-based start-up is using the proceeds from a seed funding round to prepare for iron bird ground testing as it works towards being able to support a flying prototype in around two or three years from now.
The company says it is now in early talks with aircraft developers who may have an interest in deploying a propulsion system that would be the first aviation application of magnetic levitation. It also recently announced a partnership with GE Additive’s Addworks unit to develop additive manufacturing technologies and materials for the Hyperdrive.
Maglev Aero’s technology builds on an existing VTOL aircraft concept known as an annular lift fan. While many of today’s eVTOL aircraft designs feature small propellers powered by multiple electric motors, the company is proposing to use a pair of significantly larger, counter-rotating lift fans centered around the aircraft’s fuselage, forming a huge ring-shaped duct.
Ordinary propellers have blades fixed to a center shaft, while Maglev Aero uses a rim drive design. The outer sections of the fan blades—which it says are the most productive from a lift point of view—are mounted to the outer rim, which functions as a rotor. The company also maintains this architecture will result in significant but as-yet-unspecified noise reductions compared with currently in-development multicopter or lift-and-cruise eVTOL vehicles.
In the context of high-speed railways, magnetic levitation (maglev) systems use magnets to lift a train up off the track and propel it forward. With no friction to slow it down, the train can glide along the track at higher speeds and with more efficiency. Rail services with maglev technology are already in commercial operation for high-speed airport shuttle services in China and South Korea, and a new line is being developed in Japan to connect Tokyo and Nagoya.
Magnetic Levitation Promises Friction-Free Lift and Less Noise
In Maglev Aero’s case, the magnetic “track” is an array of magnets in the circular duct that houses the rotor. The magnetic circle essentially functions as a guide rail for the rim to which the blades are attached. As the bladed rim “levitates” inside that circular duct, it can spin without any mechanical friction.
Traditional electric rotors convert electricity into mechanical energy, producing torque around the rotor’s axis to spin a propeller. The Hyperdrive instead uses electricity from the batteries to power electromagnetic propulsors in the outer rim, which use magnetic fields to control the spinning of the rotor.
According to Maglev Aero, the Hyperdrive concept could be scaled and adapted for integration with multiple new aircraft designs, with varying numbers of blades and thrust output. One of its proposed concepts shows a delta-wing airframe with a passenger and flight deck compartment at the front and the propulsion unit pivoting on a gimbal to transition between vertical and horizontal flight modes. The gap in the center of this configuration leaves more space for carrying an additional payload.
Among the unknown or undeclared aspects of the Hyperdrive concept are how its weight might compare with the dispersed electric motor and rotor/propeller combinations that are common for existing eVTOL airframes. Also, Maglev Aero isn’t yet ready to reveal how many electric inverters its system might feature in different applications. It says that it holds 21 patents for various aspects of the propulsion system.
However, the company claims that its approach will deliver a robust level of system redundancy, saying that it could incur two or three concurrent inverter failures without losing aerodynamic thrust from any of the blades. “This is in contrast to multi-rotor distributed electric propulsion architecture, which upon a failure, often requires the spinning down of the opposite side rotor to maintain thrust and torque balance, resulting in lower aerodynamic authority during a failure, and in some cases intolerance to multiple failures,” the company said in a written statement to AIN.
Maglev Aero has been operating in stealth mode since 2022 and holds 21 patents with more applications filed. Its co-founder and CEO is Ian Randall, an aerospace engineering graduate who has previously worked on cloud-computing applications and high-speed motorbikes. His father Rod Randall, who is the company’s co-founder and chair, has been active in the private equity sector after previously holding senior management roles at Bell Laboratories and Lucent Technologies.
The company’s early fund-raising efforts have drawn support from technology investors including Breakthrough Energy Ventures, Material Impact, Stage 1 Ventures, Grit Capital, and Moai Capital.
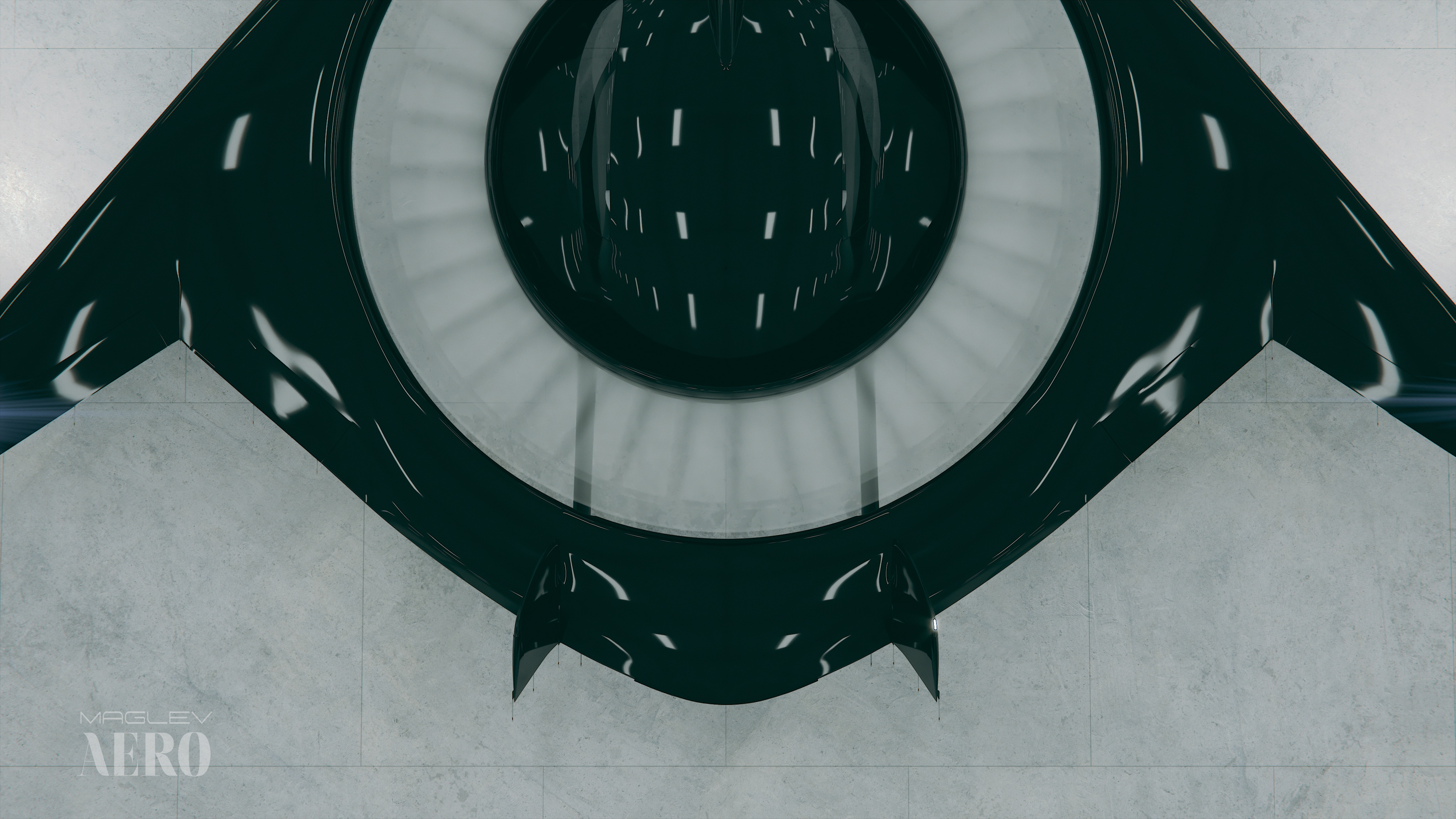